Less twist, more cuddle feeling
New zero-twist towel from KARL MAYER pushes the range for the premium segment
In June 2021, KARL MAYER launched its TM 4-TS EL terry knitting machine with the new working width of 210″ and in a gauge of E 28 in China, and shortly afterwards the textile experts at the Chinese subsidiary developed a first new product on the newcomer. The work involved processing Solucell, a twisted cotton yarn with low twist and environmental benefits over conventional counterparts, into a snug zero-twist towel article. The innovative product is softer and more compact than previous terry fabrics, perfectly meeting the current market demand for high-quality offerings.
Quality comes before price
For a long time, quality of life in China was associated with the purchase of high-priced, latest models of cell phones, cameras, computers and the like, but now people are rediscovering their love of details, such as cozy home textiles. Towels in particular are in daily use and closely associated with a pleasant everyday life. On the domestic market, absorbent bathroom products were traded for years as low-price items. In the recent past, however, purchasing behavior changed. Consumers purchase new towels more often and pay more attention to their quality. In addition, the demands placed on the product are increasing. It’s no longer just the basic functions – cleaning and drying – that are in demand, but a soft, full handle, a variety of colors and different styles. The trend shift away from price orientation towards quality and brand competition is being given new impetus by the new development from KARL MAYER.
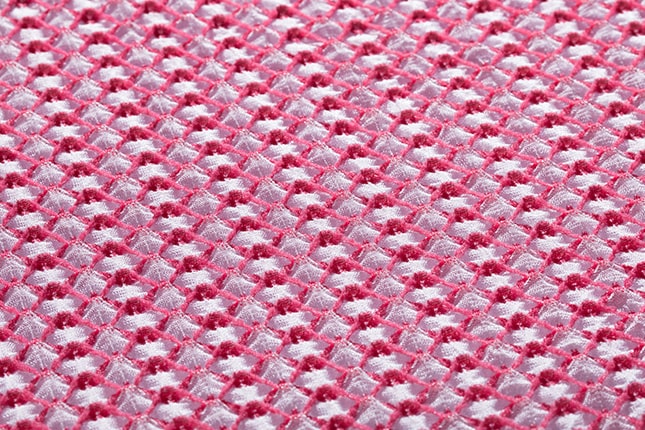
Soft, voluminous and durable – premium quality terry towels
The new article is based on the proven double face design for terry fabrics. The basic design here consists of a pillar stitch-weft lapping combination implemented by the GB 2 and GB 3 ground guide bars, which provides stability in the longitudinal and transverse directions. GB 1 and GB 4 are responsible for the terry loops on both sides. In combination with the yarn selection, the loops form a uniformly voluminous, soft surface. GB 2 processes polyester. GB 1, GB 3 and GB 4 were threaded with a combination of cotton and Solucell. The cotton content of the finished product is just under 94%. The use of Solucell results in terry loops of pure cotton, with low twist and linear density. The yarn material is fluffier than the previously used highly twisted cotton yarns and enables an extremely soft, even surface as a quality predicat.
The machine gauge used has further positive effects on the quality. Due to a configuration in E 28, the TM 4-TS EL produces fabrics with a high loop density, which ensures a full, compact handle. The terry loops are also firmly interlaced into the fabric ground. This allows the towels to be used for a long time without any loss of quality. A sample of the new zero-twist towel can be found in the Pattern section of this issue of „Kettenwirk-Praxis“.
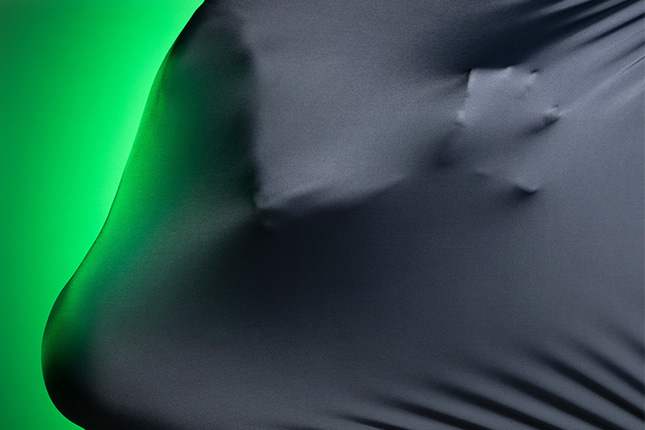
Processing without restrictions
There are many types of home textiles, and depending on the end use of the products, different processes have to be combined in their manufacture. When it comes to the production of terry fabrics, the TM 4-TS EL is an efficient and universal machine. The all-rounder processes spun yarn in gauges ranging from Ne 60 to Ne 12, and is suitable for the production of towels, bathrobes and other bathroom articles. Equipped with four guide bars and electronic guide bar control, the TM 4-TS EL meets the most diverse market requirements. The machine also impresses with its ease of operation, reliability and excellent price/performance ratio. During production of the new zero-twist towel, the intended maximum speed of 800 min-1 was achieved without any problems.
To extend operating time without changing beams, the warp beam support can be modified to accommodate beams with larger flange diameters. For GB 1 to GB 3, 40″ warp beams are possible. GB 4 can be equipped with the yarn material of warp beams with 50″ flange diameter.
Flexible warp preparation
For the production of warp beams, KARL MAYER has the right direct warping machine on offer in the form of the ISO COTTON. The model is available in ISO COTTON 21/40 and ISO COTTON 84/40 versions. The larger machine produces warp beams with dimensions that are also common in weaving.
In addition, warp beams from warp preparation systems for weaving can also be used on the TM 4-TS EL. KARL MAYER offers the appropriate warp beam support and suitable technology for this purpose: a modification kit for existing WARPDIRECT and BENDIRECT models. The modification option should be of particular interest to manufacturers of woven terry fabrics. Unlike weaving, no sizing and desizing is required for warp knitting. This saves chemicals, water and energy. Moreover, warp knitting machines are more productive than their technological counterparts, air-jet looms.
Further work already planned
KARL MAYER’s textile product developers have gained extensive experience in the field of terry knitted fabrics, particularly with regard to the perfect match between the gauge and the yarns used, and in terms of the design of the knitted structure. In their work, they focus on the appearance as well as on the performance and practicability of the towel. In a next step, the textile experts want to process functional antibacterial yarns on the terry knitting machine, thus, promoting the hygiene aspect.
More lapping variety, more shape power
New HKS 2-SE PLUS twill stitch fabrics are adding power to the lingerie and sportswear business
At the end of last year, KARL MAYER added the HKS 2-SE PLUS to its range of products for processing elastane; the first trials were completed shortly afterwards to test the new patterning possibilities it offered. Thanks to a modified knitting motion, the newcomer can not only implement conventional elastic locknit and 1 x 1 counter lappings, but twill stitch variations too. The ground guide bar GB 2, which processes elastane, may work the two-needle-overlap.
Incorporating the elastic material as a two-needle-overlap produces a fabric with a high modulus, a plump feel and a silky surface, as tests carried out by KARL MAYER’s textile product developers have demonstrated. The textile specialists produced various articles on the new HKS 2-SE PLUS with a twill stitch 1 x 2 lapping and a 2 x 1 lapping as combination partners. A polyamide filament yarn was used to implement the 2 x 1 lapping through the GB 1. The twill stitch 1 x 2 lapping was made with open and closed loops, and worked in equal lapping in the underlap and in counter lapping in the overlap, and vice versa for the 2 x 1 lapping.
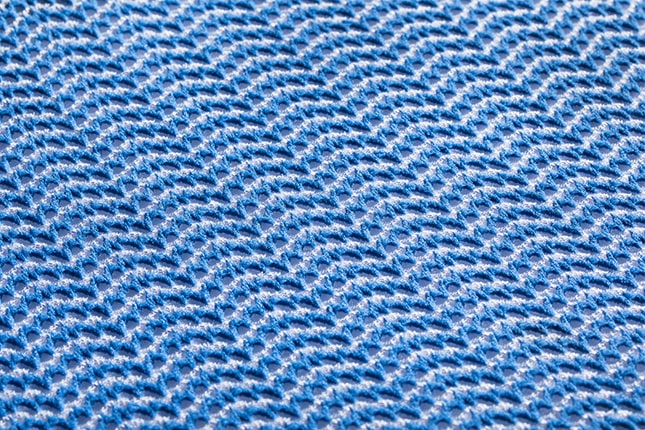
When comparing the resulting variants with a standard locknit structure – also produced on the HKS 2-SE PLUS and with the same yarn – clear differences can be seen. With a weight per unit area of between 243 g/m² and 253 g/m², the twill stitch 1 x 2 articles are noticeably heavier than the standard elastic fabric, and the elastane content is also higher. The difference is around 12%. The new elastic twill fabrics are extremely powerful and resistant to elastic deformation. They are soft against the skin, drape well and dry quickly. Thanks to this performance, fabrics featuring this modelling stretch are a promising innovation, particularly for the manufacturers of shapewear and sportswear, swimwear and lingerie articles. What’s more, the product range of the HKS 2-SE PLUS is effectively expanded. To produce the fabrics, the guide bars simply need to be adjusted using predefined settings options.
New patterning dimensions
with the HKS digital generation
HKS 3-M ON demonstrates
maximum flexibility in warp-knitted fabric design
With the HKS 3-M ON, KARL MAYER has initiated the changeover of high-performance tricot machines to the digital generation. The subsequent patterning trials at the premises of the innovative world market leader confirmed the exceptional performance of the newcomer. The HKS 3-M ON works with lapping data that can be purchased online via KARL MAYER’s WEBSHOP SPARE PARTS, and loaded immediately thanks to the machine’s networking. This means that articles can be changed in a matter of seconds without mechanical intervention. The new HKS does not need any pattern discs, but achieves the high working speeds typical of mechanical guide bar drives. The innovative machine thus contributes to improving production performance.
Article changeover made easy
In the first patterning projects, KARL MAYER’s textile product developers produced conventional basic articles, such as marquisette and flag fabric. They used the standard repeat length of up to 36 stitch courses – an increase of 12 stitch courses compared with the HKS 3-M model with pattern disc drive. All patterns could be produced with maximum efficiency and quality and changed quickly without any technical effort. There was no need for any manual intervention. Simply load the required lappings for an article via SwapKnit 36 or SwapKnit 36 Flat from the KM.ON cloud and production could start, with optimized machine data for maximum operating speeds.
Subsequent trials produced patterns with repeats of more than 36 stitch courses. The web-based software k.innovation CORE from KM.ON was used for this. With regard to the design, KARL MAYER’s textile specialists opted for variants with sophisticated crinkle looks. Articles with the crepe-like surfaces had already been successfully produced on an HKS 4-M EL in E 28. /1+2/ Now an HKS 3-M ON in E 32 was used, with the same material. In GB 1 and GB 2, a wrapping yarn made of polyamide with elastane in the core was processed. When relaxed, the two-component material gives rise to distinct plastic surface structures. GB 3 produced the fabric ground and alternated between polyamide and polyester feed. When polyester was used, targeted cross-dyeing resulted in sophisticated two-tone coloration of the three-dimensional goods. The relief effects are strongly pronounced due to the use of two ground guide bars.
In addition to the look, the performance of the items is right with the concise crinkle design. In clothing, they offer freedom of movement and a good fit due to their high elasticity. The three-dimensional structure also creates distances to the skin, which ensures a high climatic wearing comfort.
To be continued
Encouraged by the results of their processing trials, KARL MAYER’s textile product developers are implementing further pattern ideas. The focus here is on the fabric ground. “We want to make the ground structure more varied, for example, combining open and dense areas to achieve openwork looks,” says Jürgen Wohlrab, product developer for textile technology at KARL MAYER. „Kettenwirk-Praxis“ will continue to report.