The automation of spinning mills has been the focus for years and the process has become much more individualised. With the Autoconer X6 product family, Saurer provides numerous options for optimally automating the winding department in a customer-specific manner, using state-of-the-art technologies.
Tailor-made automation solutions
Three different levels characterise bobbin feeding and handling in the winding department: typically, with the type RM machines, operators do the bobbin feeding manually. For automatic bobbin feeding and material flow automation, type D and type V are available, which raises the automation level enormously. Type D works as a stand-alone machine. Type V is the direct link of the ring-spinning machine and winder, no manual bobbin/tube transport or handling between spinning and winding is necessary.
Different automation technologies, such as tube stripper or bobbin-tube extractor, are available for tailor-made automation. Linked systems can be individually designed with a direct link, underfloor link or very flexible Multilink.
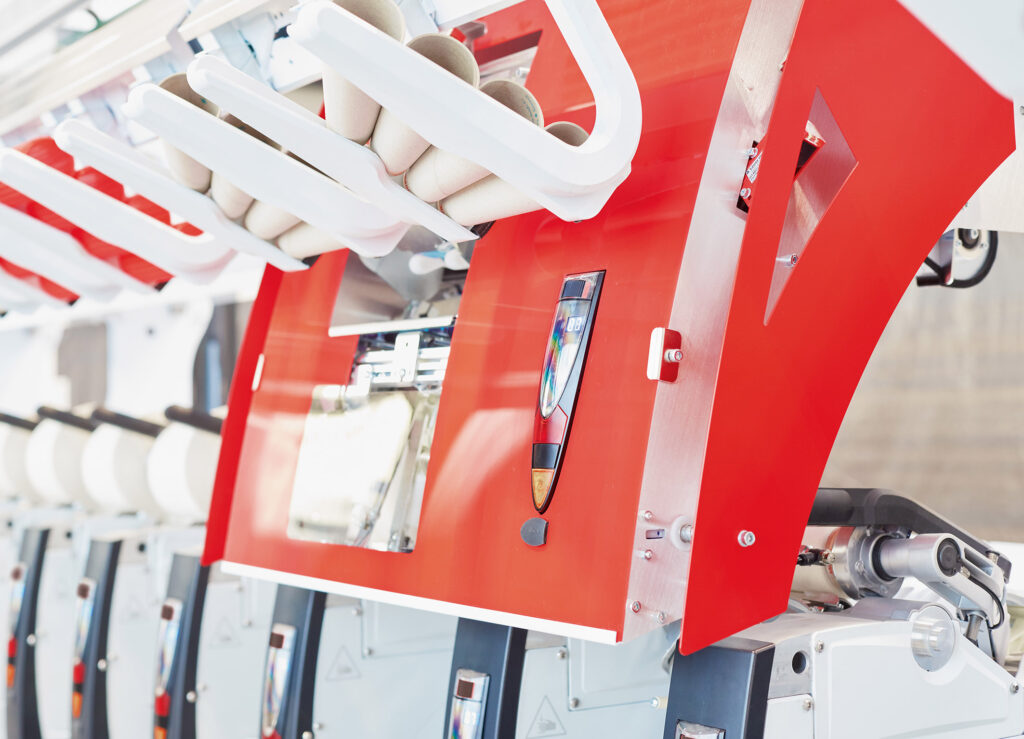
Intelligent material flow
The Autoconer X6 Bobbin Cloud material flow, characterised by self-optimising, fully software-controlled bobbin and tube management, is based on the state-of-the-art RFID technology. Here there is no need for the operator’s intervention. Additionally, in type V, online quality control with SPID is possible. In type D, the Q-Package offers different options for material lot changes and alarm bobbin management, which the system carries out independently of the operator.
Automation of package handling
Package handling on the Autoconer X6 is not just simple package doffing: the doffer X-Change supports the operator with its additional functions, such as multitube handling, empty tube strategy and tube check. These integrated, intelligent monitoring functions mean that personnel need to exert considerably less effort and can benefit from more ergonomic package handling.
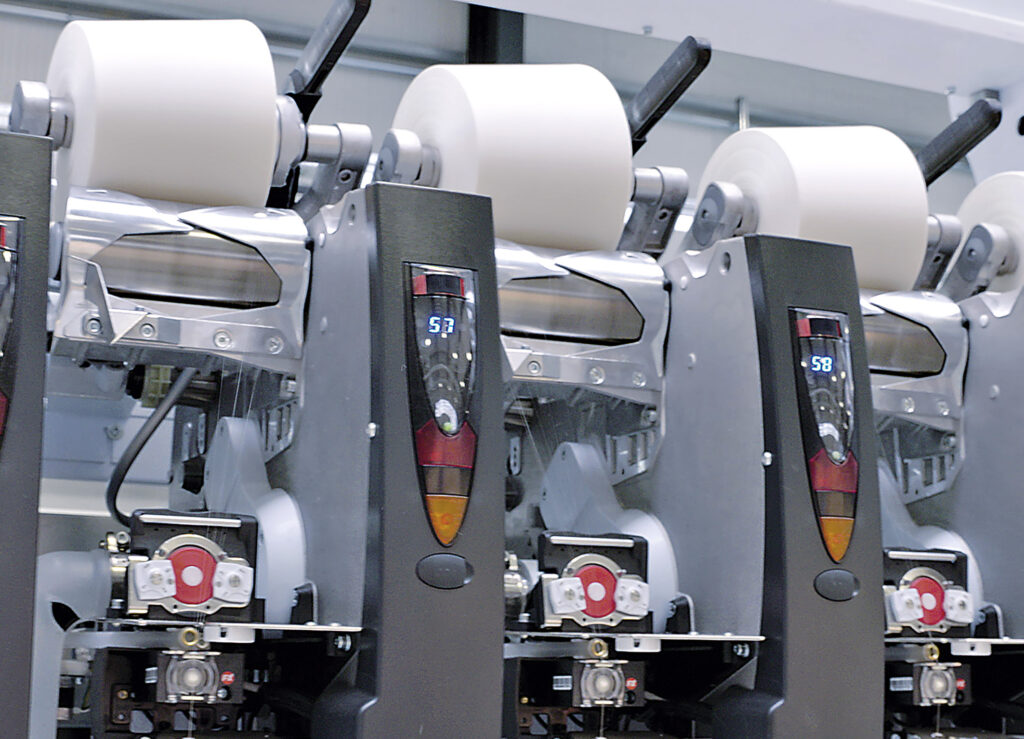
Simplified and smart winding process
Central settings of winding parameters, intelligent autocalibration functions and sensor-monitored process sequences, such as Smartcycle and Smartjet, offer operators excellent support in reducing their operating effort and minimising labour-intensive work on each winding position.