Sajjad Ahmed Qureshi highlights energy savings of 5-7% and 500 tonnes of reduced carbon footprints annually with Mahlo Atmoset. Mahlo provides machinery for processing, measuring, and controlling fabrics, to control and refine garments and cloth to your individual needs. Their expertise stretches for several decades, and their world-class manufacturing and continuous investment in R&D bring forward new and better measurement solutions for customers through collaboration and strong partnerships.
With over 77 years of industry experience and expertise, Mahlo is a secure partner for the future and many major textile brands trust Mahlo’s long-lasting experience in online process monitoring and control technologies for the textile industry. Mahlo focuses on savings in the textile sector. To find out more about the sustainability aspect of Atmoset, TEXtalks International talked with Sajjad Ahmed Qureshi. Director of Sustainability IE & Projects at US Denim Mills (Pvt) Ltd. Currently, four new units of Atmoset are purchased by US Denim.
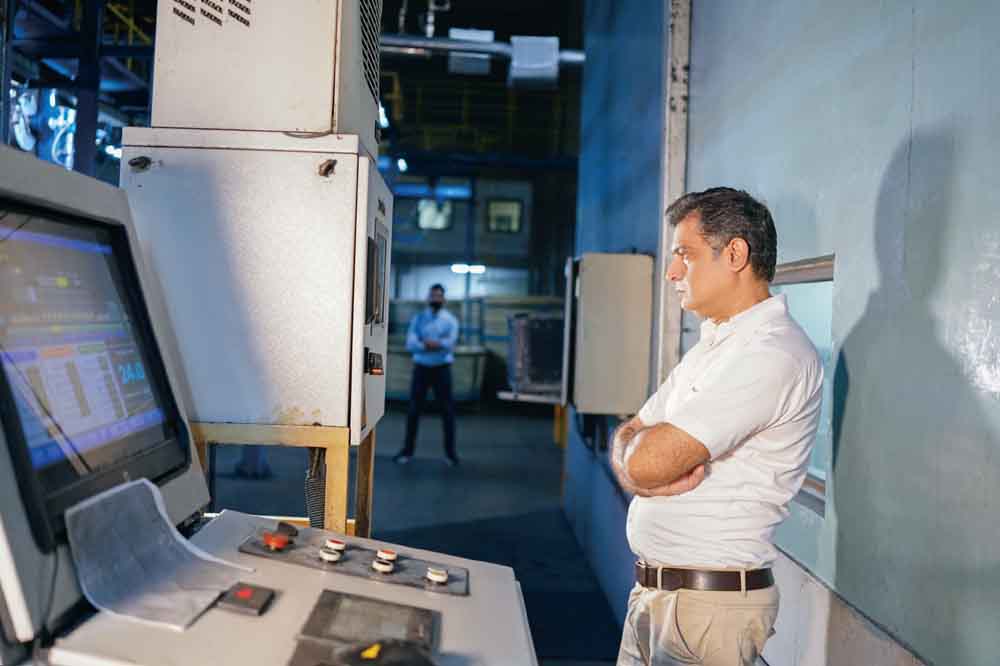
TEXtalks: Would you like to give a brief introduction about US Denim Mills?
US Denim is a Pakistan-based fabric mill supplying denim to fashion industry companies that need absolutely reliable quality and delivery at competitive prices. We constantly improve to remain state-of-the-art and sustainable in all our processes and as a product innovator, customers can be confident in partnering with us to achieve fashion leadership. Our history goes back to five decades and for over 17 years our company has been working with brands all around the world.
TEXtalks: What measures is US Denim taking to stay at the forefront of sustainability in its textile processes?
At US Denim, sustainability is our prime objective. We have been working on sustainability for many years. 2019 was our starting baseline for the new initiative and we considered it our main goal to be as environmentally friendly as possible. In the direction of sustainability, we have purchased sustainable equipment and trained our staff to help reduce our resource consumption. In our sustainability program, we have kept a keen eye on UN SDGs and set challenges for our team to reduce water consumption and GHG emissions. We also believe in providing our female staff with equal opportunities and an inclusive & friendly environment.
TEXtalks: When did you install the Atmoset and how many are functioning in your mills currently?
We installed our first Atmoset in 2017 to gauge the potential and benefits of the equipment in our Rope Dyeing. However, after exclusive study and assessments of the results we have ordered four more units for our facility. Through this, we aim to reap full-scale benefits and potential of our machines.
TEXtalks: As Atmoset ensures a homogeneous moisture profile, with your experience, what effect does it have on the quality of the fabric and savings?
Especially for the denim sector and process, quality plays a very pivotal role. After the installation of this system, we observed that the quality had significantly improved and there was a visible difference when compared to the previous quality.
TEXtalks: As energy becomes increasingly expensive, to what extent has Atmoset automation contributed to saving energy consumption?
Atmoset has reduced our energy consumption greatly and shortened our operational process. We have observed greater performance, flexibility, and efficiency which in return has decreased our energy usage. The drop in energy consumption of the dryers due to the optimized heat output has also lead to significant savings in energy costs.
TEXtalks: What difference do you think Atmoset units have and will make to reduce the carbon footprints of US Denim?
Through our calculation, we estimated that 500 tonnes of carbon footprints will be reduced per year. With lesser energy consumed, the environmental impact is lessened since sustainability is our main priority.
TEXtalks: What are the benefits of the Atmoset in terms of saving?
According to our calculation, a saving of 3-5% was anticipated but after the installation, we measured the savings again which amounted to 5-7% in terms of energy saving. The Atmoset has a stable and effective drying process with an intuitive user interface which provided us with optimized energy efficiency.
TEXtalks: How efficient is Atmoset for a dyeing house and what is its payback period?
Atmoset is a very efficient system and it has significantly reduced the time span of our processes and increased productivity. The payback period is almost 18-24 months which is quite feasible to cover.
TEXtalks: How was your experience with the after-sales service from Mahlo / Al Ameen?
Our overall experience with Mahlo and Al Ameen was very good and we are satisfied with the services they provided to us. We received competent services and the best technical support which was at our disposal. That being said, there is space for improvement in every field and we expect the same from them.
TEXtalks: In your opinion, how beneficial is the Atmoset for Pakistani mills?
As the utility cost of operating mills is increasing rapidly, increasing almost 3 folds more as compared to previous years in Pakistan, the Atmoset is a great investment to lower the burden of costs and resource consumption.