The Pinter Group continues its process of research and innovation, launching on the market a much awaited product: the Automatic Bobbin Lifter (ABL). The new product represents a turning point for those spinners focused on the improvement of quality in core yarns, reducing the cost of labor at same time.
Working principle of Automatic Bobbin Lifter system
The device consists in a special wedge installed between the elastane unwinding rollers, which will receive a signal from the Star-L optical detector in case of filament breakage. When the breakage occurs, the Automatic Bobbin Lifter is activated trough an electric signal, and the wedge lifts up the elastane bobbin. Therefore, the bobbin will be stopped, avoiding any contact with the surface of the unwinding rollers and blocking the feeding of elastane. The technical advantages are the ABL system which can be retrofitted on existing core spun attachments and it can be combined with OptiFil yarn breakages detector.
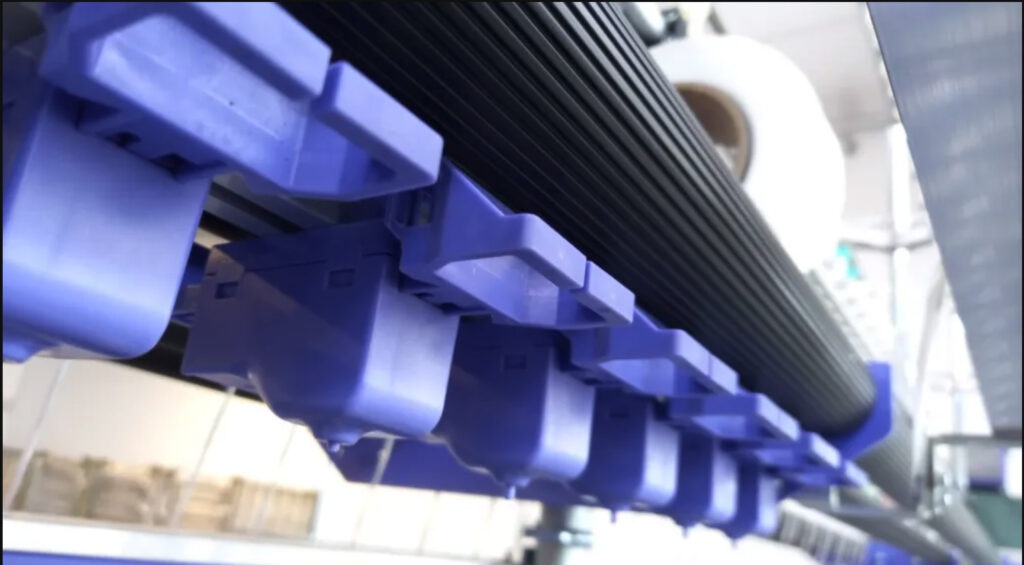
Automatic Bobbin Lifter system makes operator’s life easier, because there will be no lapping on the unwinding rollers, cots and spindles. It reduces the quantity of elastane in the pneumafil and guaranties a better quality of the yarn, because the elastane will not lap on cots. When a lap on cots happens, the same cot runs incorrectly due to the accumulation of material. This generates a displacement or even worst balance problems on the cot, which will be translated as a defect of irregularity on the yarn of the spindle close. As the risk of lapping is eliminated, the operators do not need to use knives to clean the parts involved.
It reduces labor cost, spare parts such as cradles, cots and aprons as well as pneumafil waste can be reused as it is not contaminated by elastane.